Key Sector Data |
Market Cap (Rs.crore) |
4762 |
P/E |
23.7 |
P/BV |
2.0 |
Debt/Equity |
2.2 |
ROA (%) |
2.6 |
ROE (%) |
8.6 |
EV/Sales |
1.7 |
EV/EBITDA |
9.9 | |
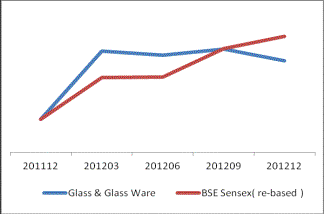 |
Indian Glass industry has been categorized into flat, container and other. Flat Glass or Glass sheet is commonly used for windows, Glass doors, transparent walls and windshields. Most flat Glass is soda lime Glass, produced by the float Glass process. Flat Glass segment comprises of float Glass and rolled Glass, which are mostly used in architectural and automotive applications. Container Glass is a type of Glass for the production of Glass container such as bottles, jars, drink ware and bowls. Container Glass stands in contrast with the flat Glass. Container Glass, which is the largest segment in the Glass sector, comprises of Glass packaging for consumer goods and pharmaceuticals. The other Glass segment mainly includes Glass used in optical and lens industry and in manufacture of cutlery, electrical insulation and various other sectors.
The domestic production of Glass sheet started showing growth from September on YoY after 13% fall at 8,253 thousand sq. meters in August due to recovery in demand from construction sector. The Glass sheet production rapidly grew 26% in October at 9,796 thousand sq. meters after increasing by 5% in September at 8,887 thousand sq. meters on YoY while, on sequential front, it grew by 10% in October followed by gain of 8% in September 2012.
On the other hand, Fibre Glass domestic production sequentially eased 2% in October to 3,667 tonnes after gaining by 10% in September on MoM. Adding to this, the pace of growth on YoY growth decelerated from 7% in September to 3% in October 2012. Fiber Glass is regularly used in protective equipment, such as helmets because of its light weight and durability. It is also used to make storage tanks, roofing laminate, door surrounds, chimneys and in pipe systems
The WPI index of Fibre Glass & Glass sheet continued to remain flat in October since April 2012 on MoM while, on YoY front, it continued to gain by 2% during the period since May 2012.
Trend in Glass Sheet Production in Thousand Square Meters |
Month |
2012 - 13 |
|
2011 - 12 |
|
2010 - 11 |
|
|
Production |
% Chg. |
Production |
% Chg. |
Production |
% Chg. |
Apr |
9250 |
14 |
8101 |
3 |
7870 |
-5 |
May |
9649 |
10 |
8745 |
3 |
8454 |
21 |
Jun |
9431 |
11 |
8499 |
2 |
8369 |
23 |
Jul |
9463 |
2 |
9286 |
12 |
8304 |
11 |
Aug |
8253 |
-13 |
9505 |
26 |
7522 |
0 |
Sep |
8887 |
5 |
8480 |
18 |
7200 |
-12 |
Oct |
9796 |
26 |
7796 |
1 |
7682 |
0 |
Nov |
-- |
0 |
9403 |
30 |
7231 |
6 |
Dec |
-- |
0 |
10845 |
24 |
8755 |
14 |
Jan |
-- |
0 |
8445 |
2 |
8242 |
16 |
Feb |
-- |
0 |
7775 |
3 |
7573 |
6 |
Mar |
-- |
0 |
9264 |
-3 |
9567 |
27 |
% Chg : Year on Year Difference |
Source : Central Statistical Organisation |
Trend in Fiber Glass Production in Tonnes |
Month |
2012 - 13 |
|
2011 - 12 |
|
2010 - 11 |
|
|
Production |
% Chg. |
Production |
% Chg. |
Production |
% Chg. |
Apr |
3940 |
23 |
3195 |
5 |
3052 |
37 |
May |
3858 |
14 |
3390 |
6 |
3194 |
77 |
Jun |
3582 |
5 |
3418 |
8 |
3152 |
87 |
Jul |
3533 |
1 |
3486 |
5 |
3305 |
75 |
Aug |
3404 |
-2 |
3463 |
4 |
3315 |
76 |
Sep |
3757 |
7 |
3498 |
9 |
3212 |
70 |
Oct |
3667 |
3 |
3577 |
10 |
3247 |
72 |
Nov |
-- |
0 |
3598 |
3 |
3484 |
85 |
Dec |
-- |
0 |
3583 |
5 |
3427 |
18 |
Jan |
-- |
0 |
3636 |
9 |
3348 |
7 |
Feb |
-- |
0 |
3713 |
18 |
3143 |
0 |
Mar |
-- |
0 |
4115 |
23 |
3337 |
3 |
% Chg: Year on Year Difference |
Source : Central Statistical Organisation |
Toughened Glass is also made from float Glass that has been specially heat treated. It is a type of safety Glass processed by controlled thermal or chemical treatments to increase its strength compared with normal Glass. It is commonly used for side and rear windows in automobiles. Toughened Glass production in India showed a growth of 2% to 2,90,168 sq. meters in October after falling by 9% in September on MoM while on YoY, the pace of growth accelerated from 20% in September to 28% in October 2012. The WPI index of laminated Glass and toughened Glass remained flat in October both sequentially and YoY basis.
Trend in Toughened Glass Production in Square Meters |
Month |
2012 - 13 |
|
2011 - 12 |
|
2010 - 11 |
|
|
Production |
% Chg. |
Production |
% Chg. |
Production |
% Chg. |
Apr |
221726 |
3 |
215975 |
8 |
199794 |
32 |
May |
222912 |
8 |
206411 |
3 |
199943 |
29 |
Jun |
283849 |
37 |
206825 |
5 |
196198 |
27 |
Jul |
220279 |
-4 |
229769 |
0 |
228953 |
46 |
Aug |
313154 |
36 |
230027 |
-1 |
231185 |
37 |
Sep |
284525 |
20 |
236899 |
7 |
222398 |
31 |
Oct |
290168 |
28 |
227477 |
-1 |
229283 |
32 |
Nov |
-- |
0 |
223139 |
9 |
205051 |
9 |
Dec |
-- |
0 |
240461 |
1 |
237474 |
26 |
Jan |
-- |
0 |
225037 |
3 |
219533 |
17 |
Feb |
-- |
0 |
213296 |
-1 |
214357 |
7 |
Mar |
-- |
0 |
222947 |
1 |
220172 |
10 |
% Chg: Year on Year Difference |
Source : Central Statistical Organisation |
The demand for the container Glass is driven by the growth in the user industry i.e. liquor & beer, pharmaceuticals, cosmetics & perfumery, food and beverages. The primary raw materials engaged in the manufacture of container Glass are sand (silica and quartz), limestone (calcite), cullet (broken Glass), soda ash, dolomite and feldspar. Indian Glass container market is estimated to be around USD 1.1 billion and is growing at the rate of 10% per annum. The per capita Glass container consumption is 1.5 kg in India lower compared to other countries.
Bottle Glass production depleted by 7% in October followed by 10% fall in September on YoY while, sequentially it showed growth of 5% to 1,01,494 tonnes in October , after plunging in last two consecutive months. The WPI index of Glass bottles & bottle ware slipped by 1% in October on MoM production while, it continued to gain on YoY to grew by 5% in October 2012.
Trend in Glass Bottle Production in Tonnes |
Month |
2012 - 13 |
|
2011 - 12 |
|
2010 - 11 |
|
|
Production |
% Chg. |
Production |
% Chg. |
Production |
% Chg. |
Apr |
108983 |
10 |
98907 |
2 |
96793 |
9 |
May |
120754 |
18 |
102272 |
5 |
96995 |
7 |
Jun |
119911 |
20 |
99757 |
9 |
91198 |
1 |
Jul |
121525 |
23 |
99178 |
6 |
93784 |
-3 |
Aug |
111571 |
4 |
107205 |
17 |
91850 |
-6 |
Sep |
96884 |
-10 |
107348 |
14 |
93813 |
1 |
Oct |
101494 |
-7 |
109669 |
14 |
96424 |
7 |
Nov |
-- |
0 |
106834 |
11 |
96404 |
10 |
Dec |
-- |
0 |
111360 |
11 |
100404 |
3 |
Jan |
-- |
0 |
112499 |
9 |
102821 |
6 |
Feb |
-- |
0 |
106158 |
19 |
89227 |
1 |
Mar |
-- |
0 |
110733 |
3 |
107118 |
6 |
% Chg : Year on Year Difference |
Source : Central Statistical Organisation |
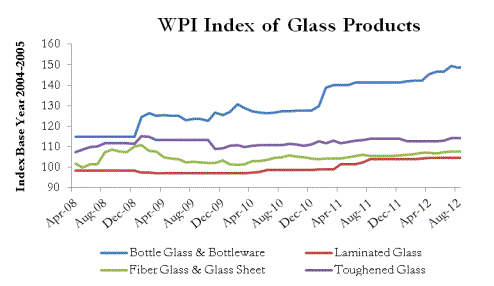 |
Soda ash is one of the major raw materials in the manufacturing of Glass. Its cost constitutes about 30% in production of Glass products. Major manufactures of Soda ash in India are Tata Chemicals, Gujarat Heavy Chemicals, DCW and NIRMA. They continue to rule the Indian market by fixing the prices of soda ash. Soda Ash prices showed growth of 3% at Rs.32 per Kg in December after falling continuously since April 2012 on YoY while, it also grew sequentially 16% during the period.
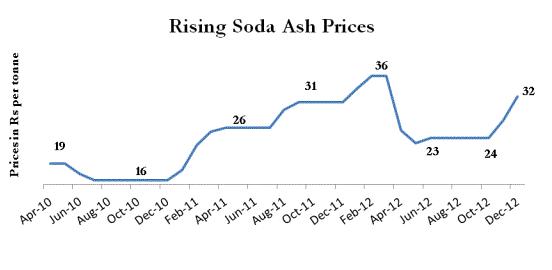 |
Asahi India Glass (AIS), India's largest integrated Glass company, manufactures a wide range of safety Glass, float Glass, architectural processed Glass and Glass products. AIS total turnover registered meager 6% growth at Rs.435.88 crore for the quarter ended September 2012 on YoY. The performance in the quarter have been significantly impacted due to external events like drop in sales led by the MSIL strike and huge increase in the costs of furnace oil , other key material . Automotive Glass segment sales increased 8% to Rs.234.14 crore while float Glass segment sales rose 4% to Rs.196.81 crore during the period. But, increase in raw material costs as % of adjusted net sales coupled with the rise in staff ,power and other expenses though constrained by foreign currency exchange gain of Rs.12.78 crore against loss of Rs.21.82 crore in corresponding period of last year led OPM to dwindle 70 bps to 9.2%. Thus, operating profit eased 1% to Rs.40.01 crore. Finally, after considering other income , interest , depreciation and tax expenses , company recorded net loss of Rs.28.99 crore against Rs.19.61 crore in corresponding period of last year. However, company articulated confidence in its recent press release of bringing back its financial performance to normal again in near future.
AIS Auto Glass caters to around 72% of the passenger vehicles segment through the OEM route and has remained a market leader in the segment. AIS Auto Glass has recently taken fresh initiatives to remove some bottlenecks and raise its capacity. The same is aimed at bringing down the overhead and freight costs. The ensuing expansion involves enhancement of direct production and supporting equipment. Total project outlay, is estimated to be around Rs.125 crore. AIS Float Glass commands 25% share in the Float Glass market. AIS expects that the growth in Float Glass segment is expected to pick up once the interest rates start softening leading to increasing demand for real estate.
Hindustan National Glass (HNG), the largest container Glass packaging solutions provider in India, net turnover decreased 8% to Rs.388.41 crore for the quarter ended September 2012 due to decline in sales volumes though limited by rise in realization and mere growth in production on YoY. Production volumes rose 4% to 2.39 lakh tonnes impacted by shutdown of Pondicherry plant for rebuild from September 15th to December 2012, price realization increased 11% to Rs.22,613 per tonne while sales volumes declined 17% to 1.70 lakh tonnes. Increase in raw material costs as % of adjusted net sales coupled with the rise in staff and other expenses led OPM to decline by 540 bps to 11.6%. Thus, operating profit declined 37% to Rs.45.15 crore. But, after consideration of other income, interest, depreciation and tax expenses, company posted net loss of Rs.28.49 crore against net profit of Rs.16.76 crore in CPLY. In order to optimize the cost, company is implementing various processes and systems across the manufacturing units. The company is sourcing power through IEX, and it has entered into long term tie ups with mine owners for captive processing and supply of silica sand. Therefore, company expects the margins to improve as the initiatives start yielding cost benefits in the coming quarters.
HNG has commissioned its Glass container plants at Naidupeta (Andhra Pradesh) and its second line of operation at Nashik (Maharashtra) with a capacity of 650 MT per day during the September and June quarter respectively. Company has commercially commenced Naidupeta plant in Andhra Pradesh towards the end of Q2FY13. Further, company is in plans to expand to 5,015 TPD by 2015 from existing 4,235 TPD of capacity (including Naidupeta). HNG acquired assets of Germany based Agenda Glass (AG) with a manufacturing capacity of 320 TPD in May 2011 and commenced operations under HNG management in August 2011. HNG expects this company's overall operations to break even in FY2013. Hence, from the extended capacities and increased capacity utilizations, management expects the production and sales volumes to improve significantly.
Piramal Glass that manufacturers Glass containers for the Pharmaceuticals, Cosmetics & Perfumery (C&P) and Speciality Food & Beverage (F&B) industry net turnover grew 28% to Rs.421.93 crore for the quarter ended September 2012 on YoY aided by significant growth across the verticals. Cosmetics and Perfumery (C&P) segment sales grew 22% to Rs.211 crore. Besides, Pharma segment sales increased 56% to Rs.106 crore on the account of availability of 255 TPD for the full period and specialty food and beverage (SF & B) segment sales improved 18% to Rs.82 crore. On the other hand , company is catering to low –end SF & B in India until the new 160 TPD Mass C& P furnace stabilizes. But , increase in power and other expenses coupled with the loss at foreign exchange against gain in corresponding period of last year, subdued product mix and price realization led OPM to drop by 1300 bps to 14.6%. Thus, operating profit declined 33% to Rs.61.56 crore. However, operating performance in the new furnace installed in April 2012 has improved compared to Q1FY13. Besides, decline in interest costs limited the PBDT fall to 29% to Rs.44.94 crore. After considering the depreciation and tax expenses, net profit crashed 68% to Rs.8.90 crore. Finally, bottom line fell 81% to Rs.4.31 crore after adjusting with minority interest. Company expects CAGR of 21-23% for FY11 to FY13 period and EBITDA margins of 24 -24.5% for FY13.
Outlook
Indian Glass industry as a whole has been impacted by the sharp rise in the cost of key raw materials accentuated by unprecedented depreciation of Indian rupees against the US dollars, a double blow on the cost front. The price of Soda ash is a major cost in the raw material segment. Higher cost of input particularly Soda ash, which constitutes about 30% of cost of production of glass products, is one of the major factors contributing to the higher cost of glass and glassware. Major manufactures of Soda ash in India are Tata Chemicals (formerly Gujarat Heavy Chemicals), DCW and NIRMA and Saurashtra Chemicals. They continue to rule the Indian soda ash market by fixing the prices of soda ash based on the landed cost of imports.
Apart from the rise in the cost of raw materials, a sharp rise in the cost of power and energy has also impacted the industry. Even though the short term growth looks pale, the long term growth of the industry is intact backed by the expected revival in auto sector, real estate sector and in the retail sector due to the allowing of 51% FDI. Growth in Float Glass segment is expected to pick up once the interest rates start softening leading to increasing demand for real estate. Finally, players who have taken initiatives to control the costs will benefit with relatively better margins.
Glass consumption growth is expected to increase in all the major sectors such as consumer goods, pharmaceuticals, automotive and construction driven by up tick in demand. The lower per capita consumption of 1.5 kg in India as compared to the other countries and the strong economic drivers for end user segments (liquor, beer, pharma, food, cosmetics etc) will boost the demand for the industry.
|