Dalmia Bharat's subsidiary Dalmia Cement has entered into a share purchase agreement with Jaiprakash Associates to acquire its cement assets spread across Madhya Pradesh, Chhattisgarh, and Uttar Pradesh with 9.4 million tonnes per annum capacity (along with a clinker capacity of 6.7 million tonnes and thermal power plants of 280 MW), as it looks to expand its domestic presence.
This deal is part of Jaiprakash Associates' efforts to pay off its lenders by selling its assets. Between 2014 and 2017, the company sold cement capacity of 20 million tonnes per annum (MTPA) to UltraTech Cement, while selling its controlling stake of more than 2 MTPA cement capacity to Dalmia Group in 2015.
Post this transaction, Jaiprakash Associates would fully exit the cement manufacturing space providing partial respite to the debt-laden company. The Enterprise Value (EV) of the deal is set at Rs 5,666 crore for 9.4 million tonnes implying an EV/tonne at Rs6,027 or around $73.
Dalmia Bharat is dominant in South and Eastern markets and this deal gels well with its agenda of becoming a pan-India player with the addition of (central India assets) of Jaiprakash with a capacity of 75 million tonnes by FY27 and 110-130 million tonnes by FY31.
In May 2022, the billionaire Gautam Adani paid as much as $10.5 billion to buy Ambuja Cements and ACC from Switzerland-based Holcim.
Cement prices continues to firm in December
With the recovery in demand, cement prices beginning to look up in most regions.All-India cement prices continue to see nominal uptrend in December 2022 with pan-India prices up ~1% MoM. Prices in South corrected by 2% MoMwhereas rest of India saw a 1-2% MoMhike in December 2022.
All-India average price growth at 3% quarter on quarter (QoQ) in Q3FY23 QTD, with the highest increase seen in East (9%), followed by South and West (4% each). The average price remained flat QoQ in the North, and there could be a marginal decline in Central India (down 0.6%QoQ).
Cement margins plummeted to record low levels in 2QFY23 due to consumption of high-cost coal and pet coke inventory. Pet coke and thermal coal prices have corrected by 25-30% from peak and energy costs should see back-ended reduction in 2HFY23. Diesel prices have been stable for the past 6-7 months; however, with recent 10-15% correction in Brent crude prices, hikes in diesel prices could be ruled out in the near term.
Cement Industry Scenario
India is the world second largest cement producer (after China) and accounts for over 8% of the global installed capacity. The three most common cement types produced in India are OPC, PPC, and PSC.
The current capacity of the Indian cement industry is ~500 million tonne per annum (MTPA) and average capacity utilization ranges between 65-70%. India's cement demand is expected to reach 550-600 MTPA by 2025, due to the increasing demand in various sectors such as housing, commercial construction and industrial construction,
India's cement industry is a vital part of its economy and employs over one million people, directly or indirectly. The industry plays a crucial role in the development of the housing and infrastructure sector of the economy.
Given the cement sector's healthy long-term growth potential, which is currentlybeing reflected in the low per capita consumption (i.e. at ~250/kg vs. global averageof ~550/kg per capita), cement demand expected to grow at a CAGR of 6-6.5% over thenext four to five years. This will be driven by good monsoon, higher farm realisationsand the government's focus on infrastructure, especially affordable housing and roadconstruction, in the run-up to general elections in India in 2024. On the cost front, therecent measures by the government (like ban on steel exports, excise duty cut ondiesel) would help in moderating the inflationary pressure. However, major costbenefit for cement companies would accrue only after structural downturn in thepetcoke/coal prices that are still trading at elevated levels.
The cement sector is likely to witness a glut of new supplies over the next three tofour yearsbased on the recent capex plan announced by majorcement companies.As per Crisil Ratings, the Indian cement industry is likely to add ~80 million tonnes (MT) capacity by FY24, the highest since the last 10 years, driven by increasing spending on housing and infrastructure activities. This would lead to fresh rounds of consolidationespecially in the mid and small sized cement players having high coststructure/bloated balance sheet. The near-term cost headwinds have already pressurisedmargins as player are unable to pass on the cost pressure due to moderation indemand in the wake of higher inflation. This has led to cement sectorunderperforming broader markets. While long-term demand is expected to stayheathy.
Thecement sector is likely to witness a subdued EBITDA/tonne in the remainder of financial year on account of continued inflationary pressures of several cost elements. The cost escalation which the sector has been experiencing since the start of 2022 has persisted as evident from the QE September 2022 results. However, there are certain green shoots indicating a probable turnaround in the upcoming quarters.
Cement demand expected to grow by 7-8% in the current fiscal (FY23), driven by the government's continued thrust on rural and affordable housing, increased allocation to infrastructure projects, revival of urban housing and commercial segment post the impact of COVID-19 over the past two years. Cement demand would also likely be boosted by the pre-election government spending ahead of the general elections in May'24.
Factors likely to aid demand:
- Urban and Rural Housing:
- Demand revival expected in real estate
- Positive momentum is likely in rural demand due to the promising rabi crop outlook
- The construction of nearly 8 million houses is likely to generate demand from the rural segment
- Infrastructure:
- 25,000 kilometres of roads are targeted in FY23
- Positive momentum is expected in urban infrastructure, Bharatmala and Metro projects
- Positive infra outlay in state Budgets
- Industrial and Commercial:
- Implementation of PLI scheme to boost the demand further
- Aggressive targets, coupled with the PLI scheme and the rising capital expenditure
- The increasing emergence of e-commerce and retail would likely push demand for warehouse
- The government's aim of 220 airports by 2025 would further boost the demand
The budgetary allocation of over Rs 9.2 lakh crore towards agriculture, affordable housing, and capital expenditure is expected to augur well for cement demand. The cement demand is expected to grow by 7-8% in FY2023 supported by strong demand from rural housing and infrastructure sectors.
Cement Industry output falls 4.3%inOctober 2022
All-India cement production (proxy for demand), as reported by the Office of Economic Advisor, Ministry of Commerce and Industry, decreased4.3% to 296.23lakh tonnes in October 2022 over a year and lower by 2.4% over September 2022.
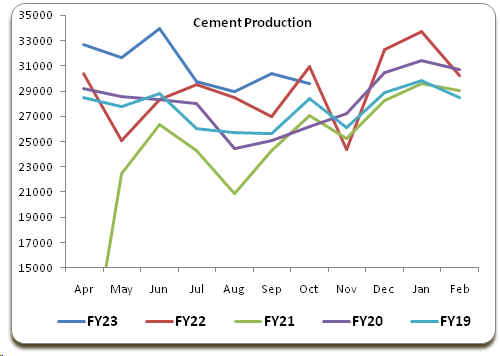
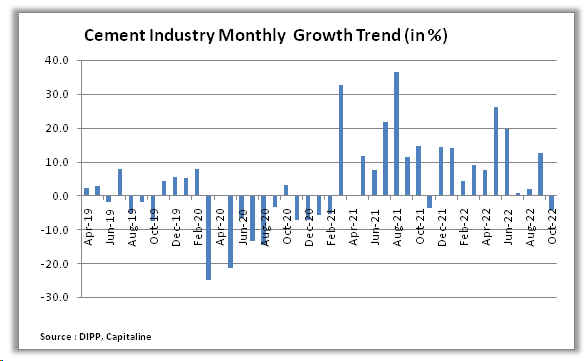
For April-October period of FY 2023, cement production increased by 8.6% to 2168.88 lakh tonnes. Cement production increased by 20.9% to 3,562.04 lakh tonnes in FY2022 as compared cement production de-growth of 11.9% to 2,945.22 lakh tones in FY 2021, de-growth of0.9% to 3,343.66 lakh tonnes in FY 2020, growth of 13.3% to 3,373.22 lakh tones in FY2019, and growth of 6.3% to 2,977.11 lakh tonnes in the FY2018.
Cement WPI for November 2022
The Cement, Lime and Plaster Wholesale Price Index (WPI), with a weight of 1.644 in the WPI, inclined 6.5% to 137.3 in November 2022 over a year and up by0.2% over month.
For April-November period of FY 2023, Cement, Lime and Plaster WPI growth was up 8.9%. Cement, Lime and Plaster WPI growth was up 4.7% for FY2022 as compared to growth of 1.1% in FY2021,growth of 4.6% in FY 2020, growth of 0.5% in FY2019, growth of 2.9% in FY2018, and growth of 0.6% in FY2017.
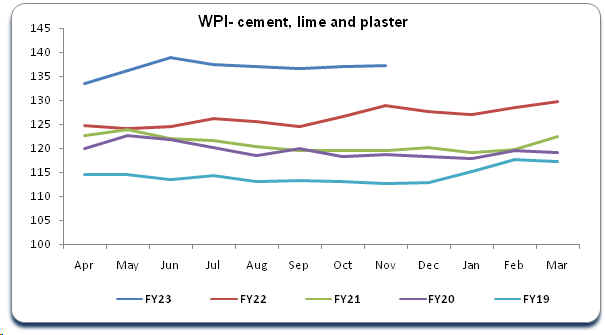
Meanwhile, the Ordinary Portland cement WPI, with a weight of 0.852 in the WPI, rose 5.3% at 134.5 in November2022 over the year and up by 0.4% over the month.
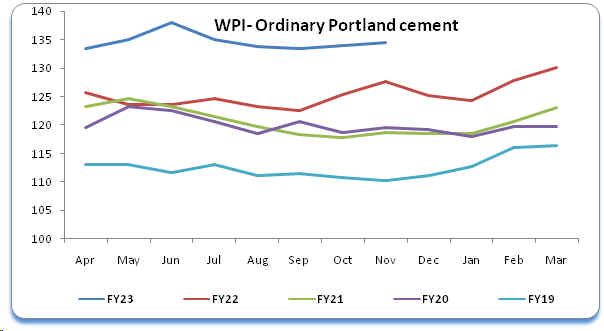
For April-November period of FY 2023,Ordinary Portland cement WPI grew 8.1%. it was up 3.9% in FY2022 as compared to growth of 0.5% in FY2021, growth of 6.6% in FY2020, growth of 1.1% in FY 2019, growth of 3.3% in FY2018, and growth of 0.8% in FY2017.
Cement demand revives as slack season ends, govt infra spend picks up
The Indian cement industry, which had been reeling under low demand, lower realisations and higher operating costs, is seeing early signs of demand revival in most regions.
Interactions with industry experts reveal that the demand revival is stronger in East and South India and is likely to be complemented by margin improvement as the price hikes become more sustainable. The cement industry had to roll back price hikes in the previous quarter for a want of steady demand.
The September ending quarter is seasonally a weak quarter for the cement industry because of monsoons when the construction activity is slack. This time the demand also remained subdued in October due to the extended rainy season in some places and the onset of the festive season when construction activity slows down. The sector witnessed a turnaround in demand from mid-November.
The non-trade segment is the likely driving force behind the current revival in demand, backed by government spending on infrastructure projects. However, the trade, or IHB (individual house builder), segment is still to take off.
The cement demand expected to record a growth of 7% in Q3FY23. The overall demand trend is likely to remain positive going into the last quarter of the current fiscal as it is the peak period for construction activities across the country. The cement industry likely to post a YoY demand growth of 10% in FY23 and 9% FY24, led by pre-election spending and strong traction in infrastructure
Outlook
Thecement industry dynamics looks positive given better demand prospects, because of the consolidation in the sector, considerable pick up in the activity both from the government side as well as from the private side in terms of construction, real estate and related activities which is definitely extremely good.
The cement demand expected to record a growth of ~10% in FY23 and 9% FY24, driven by the government's continued thrust on rural and affordable housing, increased allocation to infrastructure projects, revival of urban housing and commercial segment post the impact of COVID-19 over the past two years. Cement demand would also likely be boosted by the pre-election government spending ahead of the general elections in May'24.
With the recovery in prices on the anvil and cool off in certain commodity prices and petcoke price in particular, the margins are set to rebound.
|